AnyMind Group, an end-to-end commerce enablement platform for brands, influencers and publishers, has today announced that it is testing greater trackability of individual items throughout the manufacturing process through cloud manufacturing platform, AnyFactory. AnyMind Group will work with Fukushokukoubou Ito, an apparel manufacturer based in Japan, and upon further improvements, will expand its deployment to other manufacturers in AnyMind Group’s factory network across Asia to enable optimization of production processes and trackability of items.
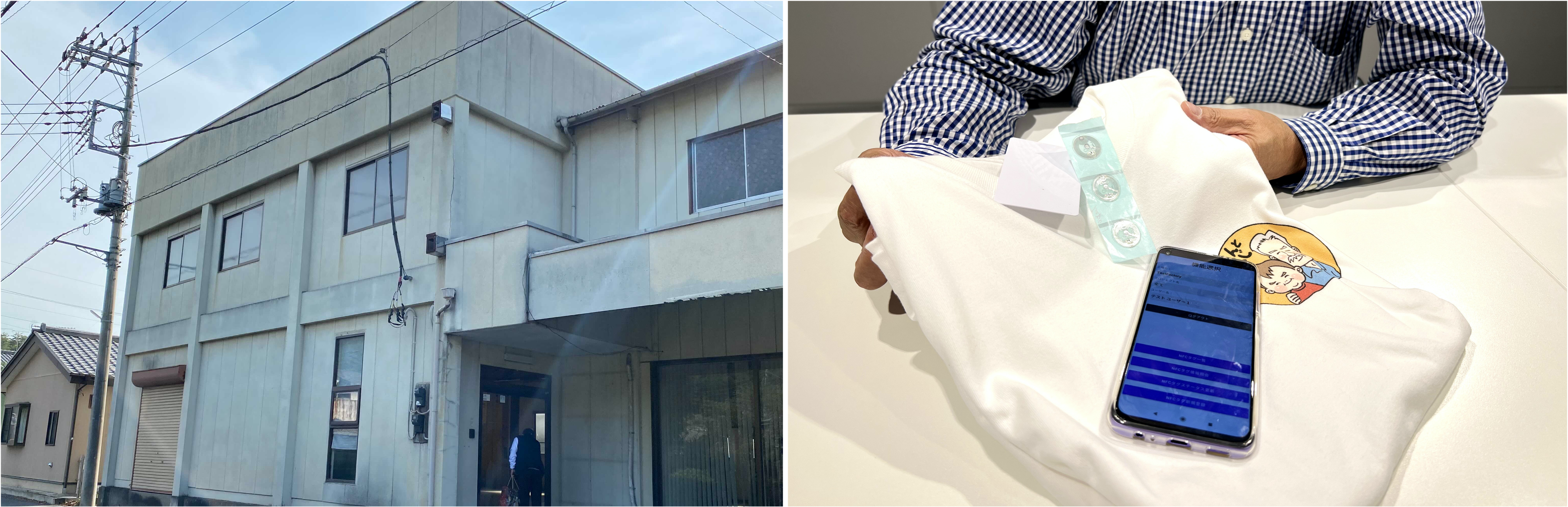
The test will be conducted through a new feature on AnyFactory called “Supply Chain Unique Tracking,” which enables the real-time process and progress tracking of individual items in the apparel production supply chain through the use of near-field communication (NFC), radio-frequency identification (RFID) tags and Internet of Things (IoT) hardware. This function will also look to facilitate the discovery of manufacturing bottlenecks, enabling improvement of efficiency of the production line, whilst concurrently sharing data on orders and receipts.
The development of this Supply Chain Unique Tracking function stems from certain challenges in the manufacturing and production process, such as a lack of visible information during the manufacturing process, unclear bottlenecks when defective products appear, and a lack of solutions linking actual production floor progress to cloud platforms that have an easy-to-understand user interface.
Kosuke Sogo, CEO And co-founder of AnyMind Group said: “Since we started our push into the wider commerce enablement space, I’ve had more opportunities to speak with manufacturers across Asia and have seen increased efforts by manufacturers to meet evolving needs. At the same time our wider offerings and customers are continuing to increase, and it’s important for us to optimize the end-to-end supply chain at an early stage or experience greater burdens as the business scales, and it will be difficult to help our customers optimize their own supply chains.”
With Supply Chain Unique Tracking, AnyFactory users will be able to visualize progress management and optimize quality, cost, and delivery by issuing a unique identifier for each item through NFC and RFID, enabling the tracking of smaller units compared to tracking using Stock Keeping Units.
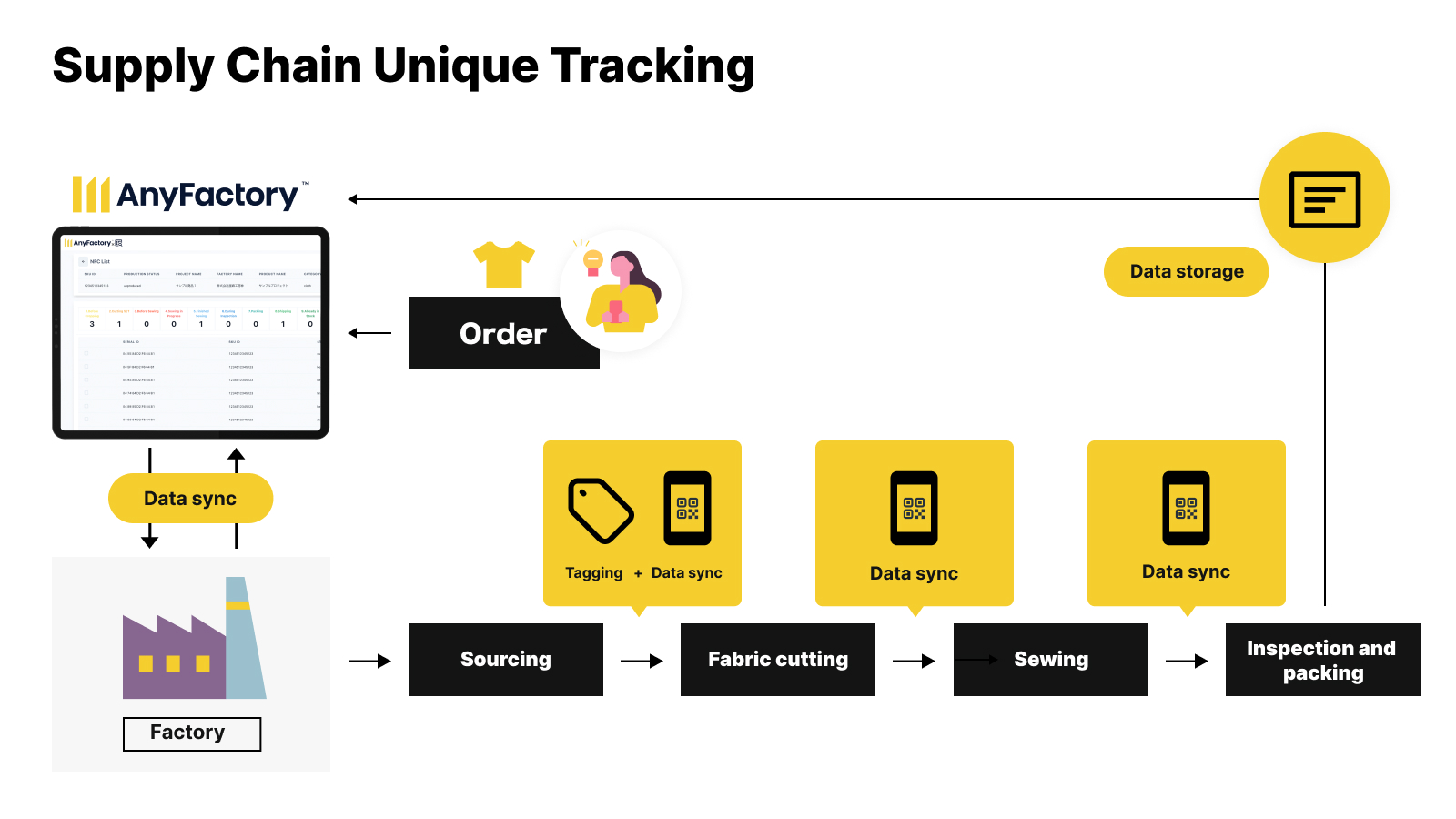
By connecting various siloed processes, from product planning to sales, in a single integrated process, greater efficiency is derived from a series of processes including procurement, manufacturing, logistics, and sales. This can also be tracked across AnyMind Group products including AnyFactory and AnyLogi, along with a connected view on the end customer’s perspective by providing a greater understanding of the current production process and logistics of items that they have ordered.

Shigeru Sakuma, CEO of Fukushokukoubou Ito, said: “I have worked with AnyMind Group in Japan on several projects, including several D2C brands, and have been greatly impressed by their attitude of promoting digital transformation at the production site itself. It was here that we also heard about the concept of Supply Chain Unique Tracking and in the course of our discussions, we felt that it was a function that would fundamentally solve the problems that had been occurring at our production sites, and that’s why we decided to open a special section for AnyFactory within our factory. In the future, we would like to work together on the development of hardware using IoT, with the aim of putting this function into full-scale practical use as soon as possible.”
Sogo also said: “We will continue our commitment to build our offerings for depth and breadth to provide exponential value for our customers. In the future, we will continue to focus AnyFactory’s development around improving the matching of businesses and manufacturers, seamless data connections for production, inventory management and logistics, and the production process itself using technology.”