AnyMindは2021年10月29日にアパレル生産を得意とする株式会社服飾工房絲 (本社:群馬県桐生市、代表取締役:佐久間 茂)と共同で、アパレル生産工程におけるアイテム一枚ごとのリアルタイムトラッキングを可能にする新機能「「Supply Chain Unique トラッキング」の実証実験を開始するというプレスリリースを発表しました。
「本質的な生産現場のDX」に向けて一石を投じ、「より良いものづくり」を実現すべく、今回生産を支援いただいている絲さんとともに大きな一歩を踏み出しました。
今回は服飾工房絲の代表である佐久間氏をお招きし、AnyFactoryの事業責任者である深見とともにインタビューを実施しました。
プレスリリースでは伝えきれない、今回の取り組みのウラ側にあるストーリーをお伝えいたします。
- 取材者プロフィール
- 「IT企業からの問い合わせ?」直感的に大きな可能性を感じた。
- ”アパレル生産は日本ではなくなる産業” だからこそ若い人たちに残せる仕組みを
- 構想を聞いた瞬間にAnyFactory専用の新工場の開設を決断
- 早速、目に見える業務効率化の成果が!
- まだまだ課題は多い。自分でもっとデータを活用できるように
- 生産現場のDXを本気で一緒に進めたい
取材者プロフィール
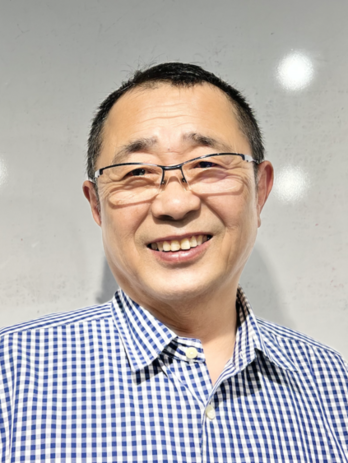
服飾工房絲
佐久間 茂 氏
代表取締役
群馬県桐生市に本拠を構え1959年創業から現在に至るまで62年に渡り、カジュアルからハイブランドまでドメスティック系を中心に幅広い生産実績を持つ服飾工房絲の代表を務める。
高校卒業以降、アパレル・ファッション・繊維業界で約40年のキャリアを持っており、業界内にも幅広いネットワークを持つ。
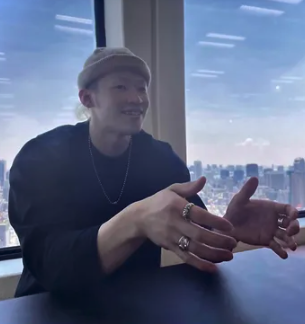
AnyMind Japan
Yuhei. F
Deputy Head of Supplier Engagement, D2C Solutions
2008年に欧州ハイブランドのテキスタイルの企画製造のニッターでの企画生産、SALESを経て、中国最大の総合商社中糧集団(COFCO)の出資を経て最大手SPAアパレル等のODM/OEMとして独立、最先端のテクノロジーを駆使してレガシーなアパレルの製造をどこよりも早くDX導入させ、年商35億規模の事業規模までの成長を実現。
テクノロジー×生産現場の技術を買われ、株式会社ZOZOに参画し、ZOZOSUITEプロダクトの立ち上げ、PBの立ち上げ、MSP(マルチサイズプラットフォーム)への展開等新規事業の開発/立ち上げを行う。
2021年AnyMindGroupに参画し、現在はD2C Solutions事業部にてAnyFactoryの責任者を務める。
「IT企業からの問い合わせ?」直感的に大きな可能性を感じた。
AnyMindとの出会いを教えてください。
佐久間:
2020年の11月くらいだったかと思いますが、最初はAnyMindさんからの電話での問い合わせでした。
六本木のIT企業からの問い合わせということで、「なんだこれは?」と思いましたが、なんだか直感的に面白そうだと感じて、取引を開始することになりました。
まずはAnyMindさんが手がけているインフルエンサーさんやD2Cブランドの生産に関する、お仕事がスタートでしたね。
主に私たちが取り扱っているのはアパレルなのですが、それらに関するプリントや刺繍などの対応の仕事を受けさせてもらうようになりました。
有名なブランドではないようにお見受けしたのですが、かなりロットの多いブランドもあり、こんな世界もあるのかと驚きましたね(笑)
そうやって考えると出会ってから1年経つのも早いもんですね、深見さん!
深見:
そうですね!
佐久間さんと出会ったころから考えると、僕たちも成長したなと思います…。
取引を始めた頃は色々とご迷惑もおかけしました(汗)
佐久間:
いやいや、とんでもない!
いろいろなブランドの仕事をさせてもらって、感謝してますよ。
そうやって、私たちにとっては通常の仕事を受けている中で、いろいろとコミュニケーションもさせてもらっている中で、AnyMindさんの目指す「オンデマンド」の話を聞いて、面白そうだなと思いました。
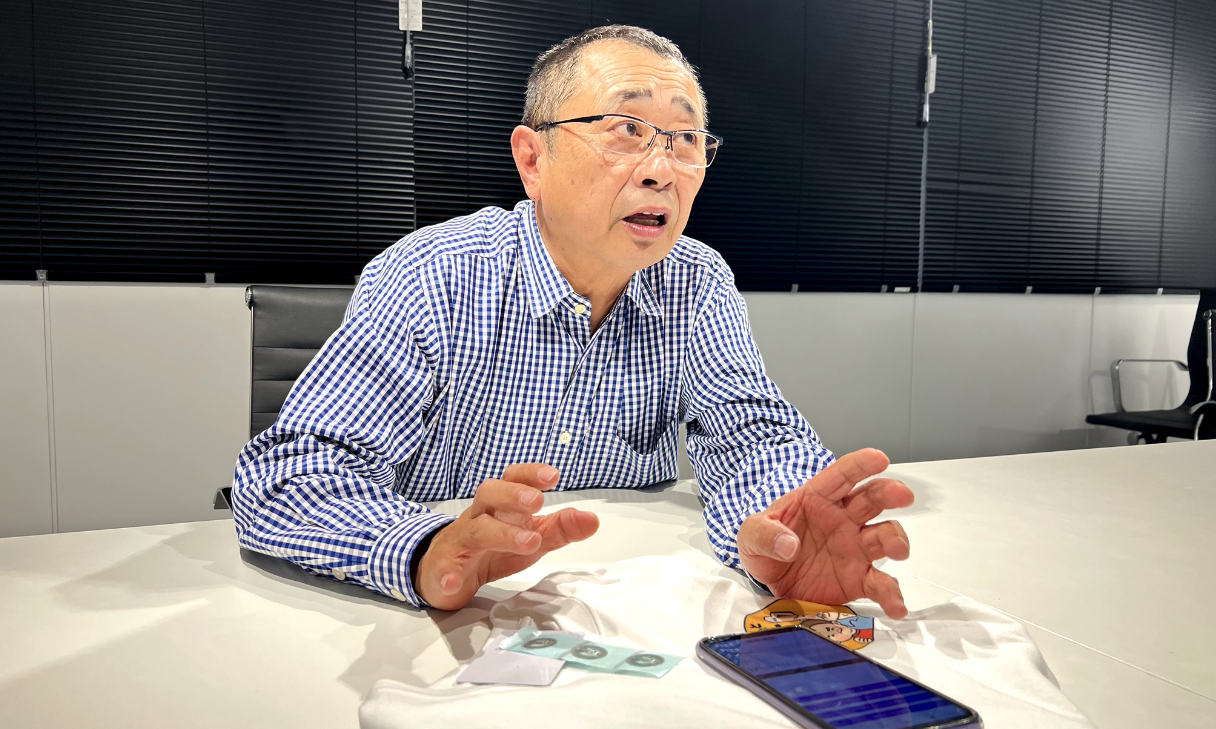
”アパレル生産は日本ではなくなる産業” だからこそ若い人たちに残せる仕組みを
「オンデマンド」での生産に興味を感じたのはなぜだったんですか?
佐久間:
そもそも、この業界に長くいる私は言うのもなんですが、”繊維業界は無駄だらけ”だと思っています。
というのも、 様々な観点があるのですが、まず当社の場合だと「百貨店」→「アパレル」→「繊維メーカー」→「生産工場」という発注の流れがあります。
全体の予算の”パイ”が限られている中で、関わる企業が多くなればなるほど、どうしても生産工場は最後になってしまうので、コストの割合的に回ってくる金額は少なくなってしまいます。
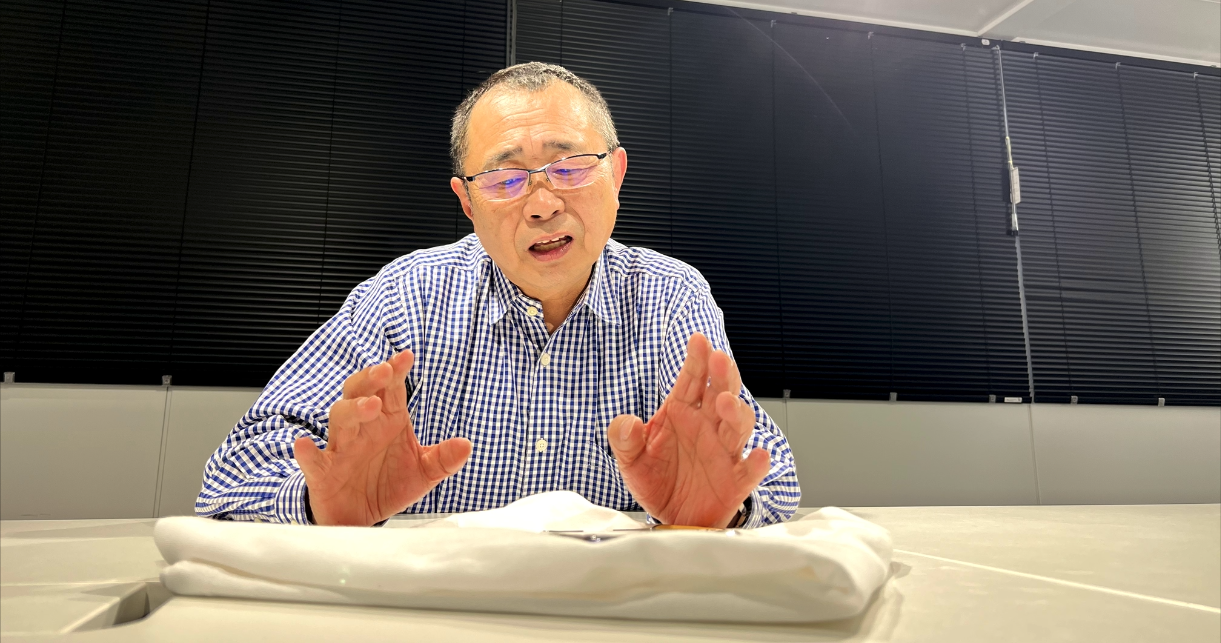
また、発注やコミュニケーションも関わる人が多い分、リアルタイムではなくなるので、「タイムラグ」が起こってしまいます。
そういった無駄はいろいろとどうしても発生してしまいます。
また、我々の方でもありがたいことに百貨店などの大きな会社から、一気に大きな発注が来ることもあります。そういった状態になれることは嬉しいですが、どうしても”波”があるんです。
それにそういった仕事はいつまでも続くものではないというのは感覚的にわかってしまっています。
正直に言うと、自分が元気なうちはこのまま生き残っていけるかもしれませんが、今後の日本のことを考えると、物価も給料も上がっていかない。
そうするとアパレルをはじめとした商品の値段も上がるはずがありません。
現場の給与水準は低く、それこそ都会のITの会社と比べると半分以下になっています。
そうすると否応なく、この”アパレル生産産業”というのは日本では必要とされなくなってしまいます。
コロナの雇用調整金などおかげもあって、なんとかなっていますが、社員に休みが多いと不安感にもつながりますし、工場というのは稼働率を上げていくべきだと考えています。
自分がただ生きていくためではなく、今後この仕事が好きで入って来てくれる若い人たちはしっかり続けていけるようなビジネスを作っていきたいと思っていました。
そこで興味を持ったのがAnyMindさんから聞いた「小品種・大ロット生産」から、需要に合わせて商品を発注して「多品種・小ロット」でもしっかり儲かる形をつくる。
受注が来てから効率的に生産をして、3日以内に納品をしていくという「オンデマンド」の構想でした。
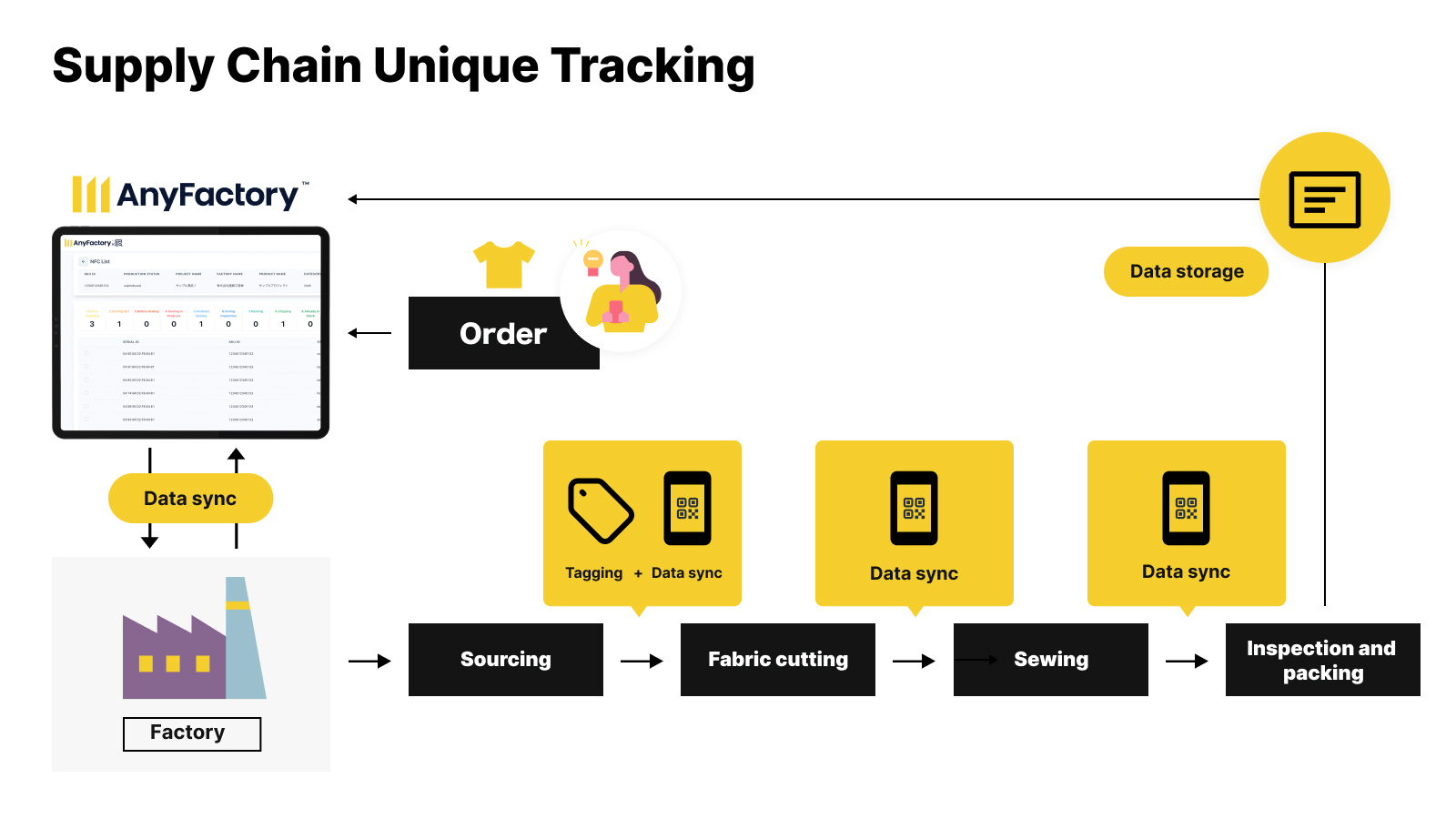
深見:
佐久間さんの感度の高さと決断力は尊敬しています。
その後、一か月も経たない間に僕たちとの取り組みに向けた新工場の開設も決断してくれて、すごく嬉しかったのを覚えています。
え!そんなスピード感だったんですね!
構想を聞いた瞬間にAnyFactory専用の新工場の開設を決断
そんなすぐに大きな決断をされて、迷いはなかったんですか?
佐久間:
そうですね、 全く迷いはなかったです。
他の会社さんやAnyMindさんからも大きなバルクでの発注はありますが、いつまでそのブランドが続いていく、もしくはいつまでも自分たちに発注してもらえるという確証はありません。
それから今、自分たちが納品した服がいつ、何枚、どんな金額で売れているかはわからないんですよね。そもそもいつから販売開始されているかもわからない。
深見さんから聞いた一枚一枚の商品の工程を追いかけることで、生産の過程を改善していくというのは、すごくユニークだなと思いましたし、結果的に工場の稼働率もコントロールでき、生産性を高めることができると感じたので、未来に向けて大きな可能性を感じました。
だから私としても覚悟を持って、一蓮托生でAnyMindさんと一緒に一つの家族のような形で進めていこうと考えました。
今後、一緒に目指していきたいのは、稼働率を上げることでも利益率を上げていく。
そうすると、納品コストも下がる。そこで次の設備投資ができる。
という形で好循環を生んでいくことです。
今、AnyMindさんほどリアルにアパレル産業と生産工場のことを考えてくれている会社さんはないと思っていますし、AnyMindさんはすごく信頼できます。今後も良きパートナーとして頑張っていきたいと思っています。
「EC」や「D2C」など、横文字の言葉も多く、難しい言葉も覚えていかないといけないのは大変ですけどね(笑)
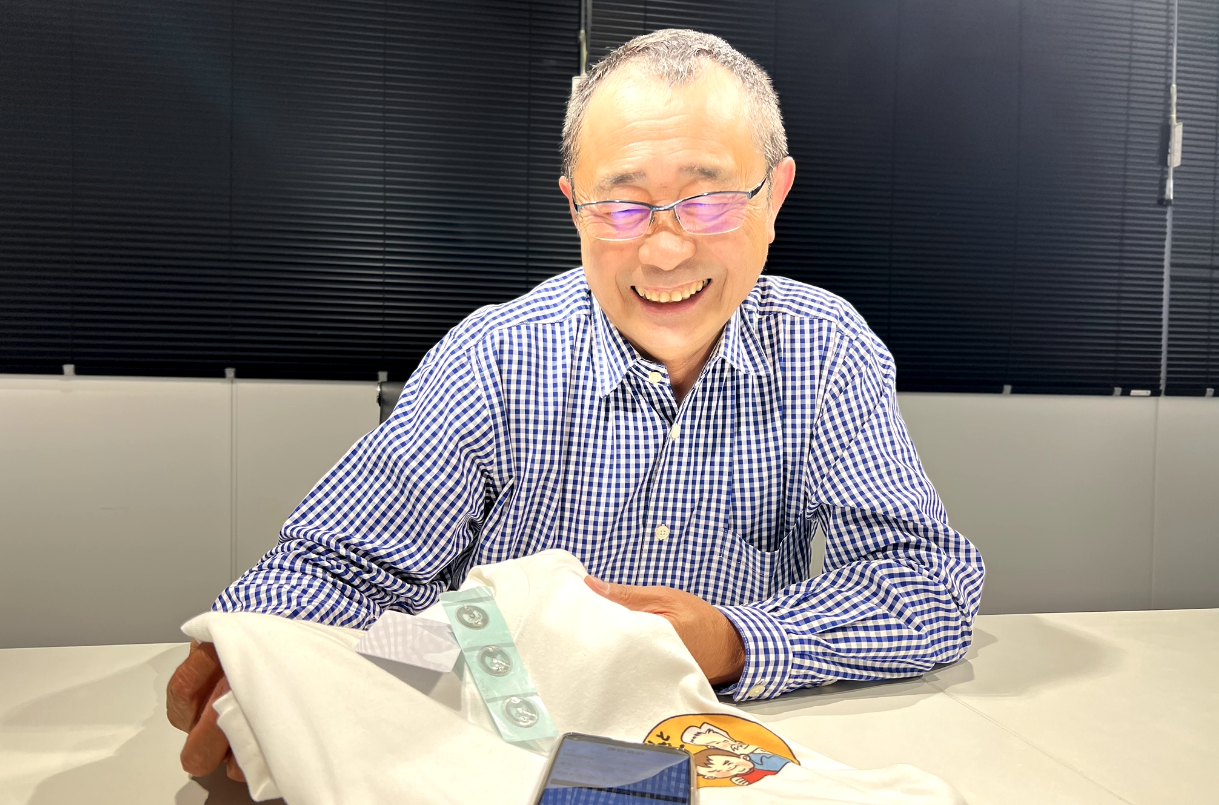
深見:
いやぁ、絶対に大変ですよね・・・。
それでも佐久間さんは常にしっかりキャッチアップしようとしてくれるので、すごく助かっています。
僕も佐久間さんほどではないですが、アパレルの生産関連の仕事をずっとしてきて、いろんな業者さんや工場ともやりとりしていますが、佐久間さんは良い意味で本当に珍しいタイプだと思っています。
生産現場にテコ入れをしようとすると、IoTやテクノロジーを活用したソリューションを入れる際にどうしても「導入コスト」はかかってしまいます。
一般的な生産工場さんだと、他の企業との兼ね合いや今のオペレーションで手一杯だということで、工数が増えるだけだと嫌がられてしまいます。
ですが、こういったまだ全体像の見え切っていない構想の段階から、ご一緒させていただけたのは感謝の一言に尽きます。
早速、目に見える業務効率化の成果が!
実際に10月から実証実験という形で稼働開始されていると思うんですが、感触はいかがですか?
佐久間:
今、新しく開設した足利のAnyFactoryの工場では、それぞれの工程でタグをスキャンすることで、それぞれの商品のトラッキングを始めています。
まだまだ始まったばかりではありますが、今後この仕組みがしっかりと実装していければ、 確実に業務効率化できるだろうなと感じています。
例えば単純なところで言うと「電話」ですね。
これまでだと、商品が今どういった過程にあるのかを確認するための電話が発注元から入ることが多かったのですが、忙しいとそもそも電話に出れないですし、電話に出ることで生産ラインを都度止めることにもなってしまうので生産性が下がっていました。
また先方も忙しかったりすると、折り返し電話の入れ違いで半日くらいかかってしまうこともありました。
電話に費やす時間というものはとても多いので、どうしても無駄が発生していました。
多い日には、1日180本の電話があることもありますね…。
それがこのトラッキングによって、スマホで「ピッ」とするだけで、インターネット上で全てわかるので、発注元からしても問い合わせなしで、状態が分かってもらえるので、無駄な工数が減ります。
これはシンプルにすごくありがたいですね。
それから、D2CブランドのようにSKUが多い場合、どのアイテム、どの色、どのサイズのことを言っているか、 何が何だかわからなくなることも増えてきました。
それに担当者も増えてきてしまうと、現場は混乱してしまいます。
ですがオンライン上で商品が明確に確認できるので、コミュニケーションのロスも少なくなったように感じます。
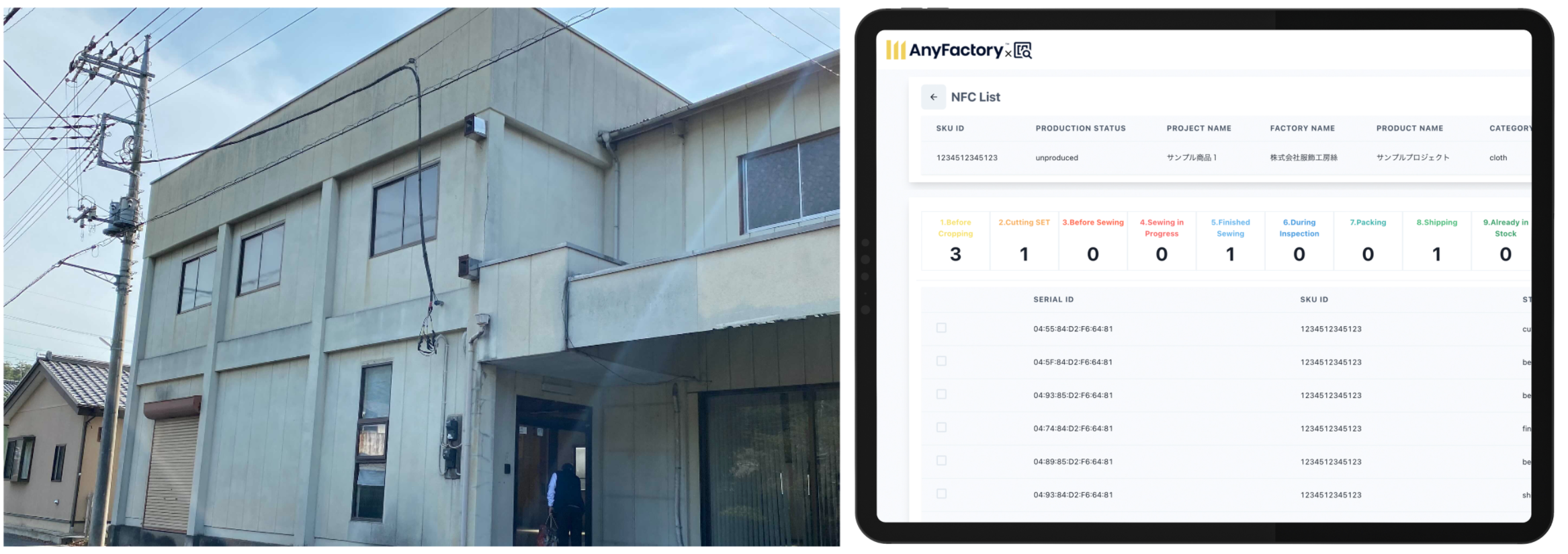
まだまだ課題は多い。自分でもっとデータを活用できるように
もうすでにかなり使いこなされているように感じるのですが、課題感などはありますか?
佐久間:
いやぁ、まだまだ全く使いこなせていないというのが肌感ですね。
データ活用をもっと自分でできるようにならないといけない。
今は逆に迷惑をかけてしまっているなぁと思っています。
イラストレーターなどが自分たちでも使えるようになると、きっともっと効率よく仕事ができるんだろうなということ自体は理解しています。
iMacを購入したり、パソコン講座なんかにも通って、こっちのレベルももっと上げて行かないといけないというのがひしひしと感じています。
Zoomで画面共有などをやってもらい、基本的な使い方に関しては教わっていきたいと思っていますね。
深見:
それはこちらからしてもお願いしたいですし、全然僕たちでできる範囲であれば、ご協力させていただきたいと思っています。
それから、今後はそういった知識がなくとも、より簡単に使っていただけるようにダッシュボード自体の開発を進めています。
佐久間:
おー!それはありがたいですね。
画面上で簡単に操作できたりなんかもするんですか?
深見:
はい、そういった簡単なプリントものであれば、ダッシュボード上で直感的にすべてオペレーションできるような体制も開発中です!
佐久間:
おー!それができるようになったら、Tシャツなんかだと一発ですね!
よりスピーディにやっていけそうです!
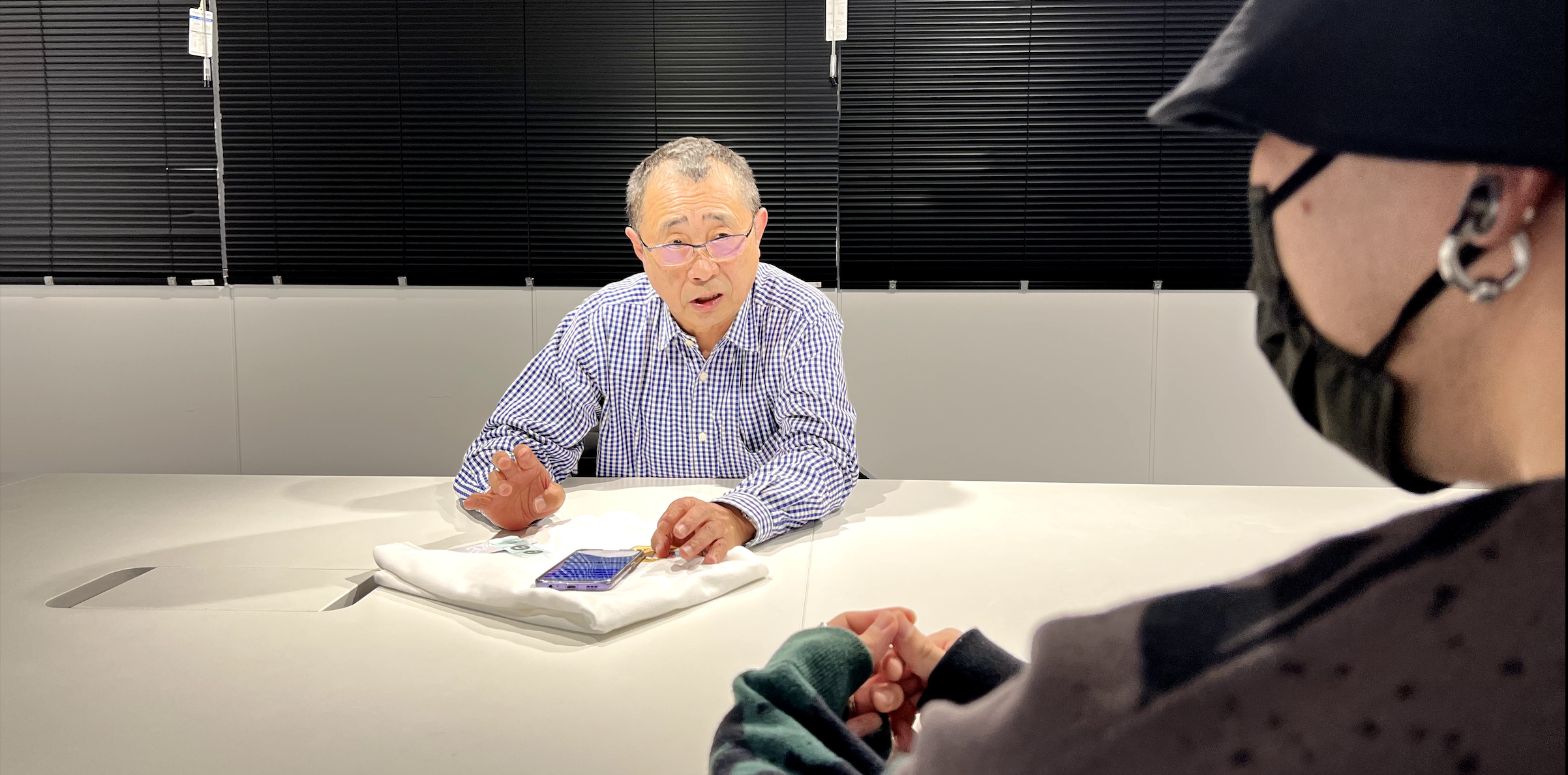
生産現場のDXを本気で一緒に進めたい
最後に一言いただけますか?
佐久間:
プレスリリースの際のコメントにも入れてもらいましたが、AnyMindさんとのお付き合いに関しては、単なる生産工場としての見方だけでなく、生産現場自体のDXを本気で推進しようとしている姿勢に大きな感銘を受けました。
「Supply Chain Unique トラッキング」の構想は、これまで生産現場で発生していた課題を根本的に解決してくれる機能であると信じていますし、だからこそ私も覚悟を持って、今回の AnyFactory 専門工場の開設を決めました。
現在まで可能性しか感じていませんし、今後はIoTを活用したハード面の開発もいろいろと教えていただきながら、どんどん進めていきたいと思っています。
この取り組みは業界全体にとっても良いことだと思うので、一刻も早い本格的な実用化に向けて、共に取り組んでいきたいと考えています。
これからもよろしくお願いします!
深見:
いえいえ、こちらこそです!どうぞ引き続きよろしくお願いします!
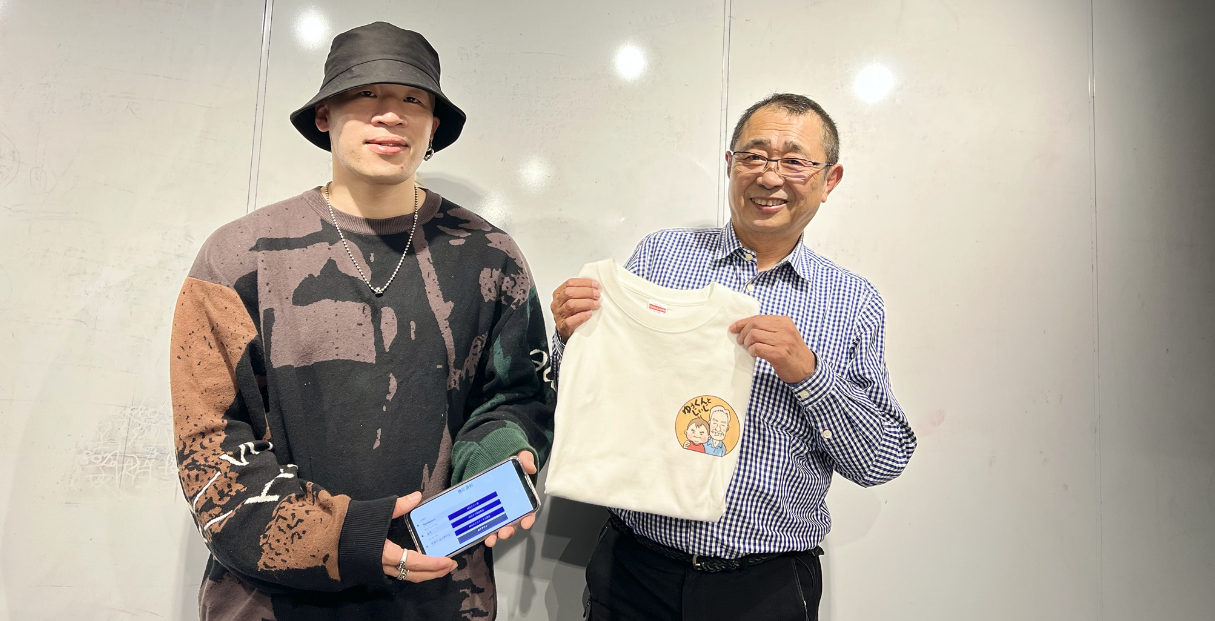